How to Choose the Right Laser Welding Machine? | 2023 Ultimate Guide
How to Choose the Right Laser Welding Machine? | 2023 Ultimate Guide
Choose the right laser welding machine from reputable laser welding suppliers. You can also find used laser welding machines for sale here. Visit us for the most diverse and specialized product selection at the most competitive prices. Place your order right now!
Choosing the right laser welding machine
A laser beam is used in the process of laser welding to join together two pieces of metal without actually touching them. This method allows for the production of welds that are both thin and have a low level of thermal distortion. Due to its speed, ability to control the welding quality during the operation, and high level of automation, laser welding is used extensively in a variety of industries, including the clinical, electronic parts, tool making, and automotive sectors, amongst others.
Why choose a laser welding machine?
There are several reasons to choose a laser welding machine:
1. They are relatively fast:
The laser allows for extremely rapid heating of the metal while minimizing the risk of deformation. Because this technology is particularly effective for welding large amounts of sheet metal, it is widely used in the automotive industry.
2. They are also technically correct
Allowing for localized, very fine, very clean, almost invisible welding. They are especially well-suited for welding small parts. Because it provides the most aesthetically pleasing welding, this type of welding is very popular in the dental and jewelry industries. It is also possible to split the laser beam into several beams to provide more accurate welding.
3. They're flexible enough to accommodate a wide range of part sizes, shapes, and materials.
Metals, including refractory metals, are the primary material for which laser welding machines are used. They can also be used to successfully weld materials that aren't metal, like ceramics and glass. They are useful for joining together pieces of widely varying shapes and sizes.
4. They are unbreakable:
With a laser welding machine, there is no physical contact between the two pieces being welded, so the equipment is protected from unnecessary wear and tear. The elimination of tool and electrode changes is an additional bonus that helps cut down on waste.
5. They can be given orders digitally:
Weld quality can now be monitored and adjusted in real time by a computer, which greatly improves productivity. Such a process allows for a great deal of automation, which in turn allows for the identification and correction of any quality issues that may arise.
However, it is important to note, that laser welding machines do have some drawbacks.
- The initial investment for laser technology is still quite high.
- When processing with this technology, precision assembly is essential to prevent laser beam deflections on the components.
- Laser welding is unsuitable for highly reflective metals because the weld is thinner than that obtained with electron beams.
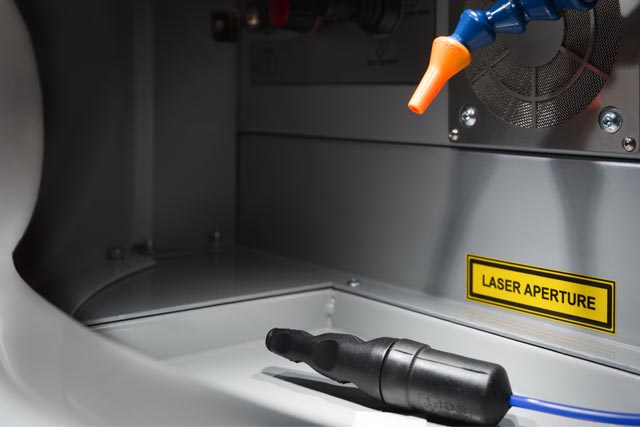
Laser welding machine advantages
Laser welding machine has advantages over other methods. With laser welding, a 'keyhole' can be created, which has many benefits. This keyhole allows heat input through the material's thickness (s). Advantages include:
1. Flexible speed.
Fast laser welding. Thin-section materials can be welded at many meters per minute, depending on the laser type and power. Lasers excel in high-productivity automated environments. For thicker sections, laser keyhole welding can complete a joint in a single pass, whereas other techniques require multiple passes. Laser welding is almost always automated, with optical fiber delivered beams from Nd:YAG, diode, fiber, and disc lasers being easily remotely manipulated using multi-axis robotic delivery systems, resulting in a geometrically flexible manufacturing process.
2. Narrow welds.
Laser welding creates high-aspect-ratio welds (large depth to narrow width). Laser welding is suitable for joint configurations unsuitable for other (conduction-limited) welding techniques, such as stake welding through lap joints. This allows smaller flanges than resistance spot-welded parts.
3. Reduced heat and distortion.
Lasers create keyholes with concentrated heat. Laser welding produces a small volume of weld metal and transmits little heat into the surrounding material, so samples distort less than with other methods. Low heat input also narrows the heat affected zones on either side of the weld, resulting in less thermal damage and property loss in the parent material.
4. Flexible Material and thickness
Steels, stainless steels, and Ni alloys, plastics, and textiles can be welded or joined with lasers. Depending on the type and power of laser, steels can be welded from under a millimeter to 30mm thick.
5. Vacuum-performed
Laser welding is done at atmospheric pressure, unlike electron beam keyhole welding, but gas shielding is often needed to prevent weld oxidation.
6. Single-sided, noncontact
Laser welding does not apply force to the workpieces being joined and is usually a single-sided process. Weld root shielding from the opposite side may be required, as with other fusion processes.
7. Welding intermittently
Lasers can make spot or stitch welds as easily as continuous welds, if suitable.
8. Versatility
With a few adjustments, a laser source can also be used for cutting, surfacing, heat treatment, marking, and rapid prototyping. The beam(s) can be delivered to the workpieces in several ways, including: One laser source can process multiple jobs by sharing a beam between welding stations. One laser source can process two areas (or the same area from opposite sides) on a workpiece by energy-sharing a single beam. Special transmission or focusing optics shape or split beams to process materials with different energy distributions.
Pulsed or continuous laser?
You have a choice between using a pulsed laser or a continuous laser in your laser welding machine. What determines which one is better to use is the thickness of the material being welded.
Pulsed laser.
It works well with lightweight, thin metals. They won't melt or become deformed thanks to this. Pulsed lasers like these are typically employed for welding sheet metal, razor blades, gold jewelry chain links, and titanium pacemakers.
This is the laser that never stops shining.
When welding thick materials, this method is highly recommended. If you have any recalcitrant metals, you should try this method. Using it on metal or a too-thin component can cause issues. The laser risks damaging, deforming, or melting the component under these conditions. Compared to a pulsed laser, it is more expensive, but it saves money in the long run.
How to choose the laser beam source?
Fiber lasers, CO2 lasers, and Nd: YAG lasers are the three primary options. Depending on the laser system you've decided to go with, different options will be available (pulsed or continuous).
1. The fiber laser.
Because of the sharpness and thinness of the beams used in this technology, work can be done in a continuous and penetrating fashion. The fiber laser, like the CO2 laser, can quickly and efficiently cut through thick sheets. In contrast to other types of lasers, it is simpler to use and maintain when it is built into a machine. Typically, this laser operates at a 25% efficiency rate.
2. CO2 laser.
With this method, a gaseous combination of carbon dioxide, helium, and nitrogen is electrically excited to achieve optimal performance in a nonstop setting. CO2 lasers, similar to fiber lasers, can quickly and efficiently cut through thick sheets. It is more popular than the fiber laser because it can more easily cut through thick steel. When compared to the fiber laser, this one is more versatile and capable of cutting through both thicker and thinner materials with ease. An average efficiency of 7% for 8,000 W is provided by this laser.
3. To be specific, the Nd: YAG laser.
All aspects of laser pulses, including intensity, duration, and profile, can be precisely managed in this way. Pulsed mode is its natural habitat. But the pulses it sends out have such a wide range of wavelengths that not all of them hit their mark and instead dissipate into heat. This laser's efficiency ranges from 3-4%, significantly lower than that of CO2 lasers (7-10%) and fiber lasers (25-30%).
What parameters should be checked?
It is important to double check a few things before firing up your laser welding machine. In order to ensure that your welding operations go smoothly, here are some standard safety measures to take.
1. Energy Adjustment
- Adapting the power to the process requires adjusting the energy level appropriately.
- Energy loss can be avoided in this way.
- Be sure your beam diameter is accurate.
- Welding efficiency decreases as diameter increases.
- The diameter of the laser beam you select should be between 0.2 and 2 mm.
2. Analyze the pulse frequencies to see if they are correct.
Higher pulse frequencies lead to lower pulse energies, which in turn leads to subpar or nonexistent welding performance.
3. Keep your eye on the shape of the laser pulses.
In order to get the best results when welding different metals, we suggest switching the waveform. Depending on the waveform chosen, anywhere from 60 percent to 98 percent of the laser's energy will be wasted, rendering the welding operation useless.
Which configuration should I choose for my welding machine?
Welding machines can be set up in one of three ways:
- Manual configuration
- Semi-automatic Setup
- Fully-automatic Setup
The following factors will determine which configuration is selected:
- The size of your production (will you be making a few items, or a lot?)
- Your preferred method of work station.
1) Welding machines by hand
- They are smaller than semi-automatic and automatic machines.
- They have either manual or automatic doors.
- The operator is in charge of the series of welded parts.
- These machines are ideal for small-scale production.
2) Semi-automatic laser welding machines:
- They're much larger than traditional welding tools.
- They have record spinners built in.
- These kinds of machines are particularly well suited to mass production.
3) Automatic laser welding machines:
- The biggest ones are these.
- The robotic systems control the part's placement beneath the laser on their own.
- The decreased need for human input is a welcome relief for the machine's operator.
- Their high quality and low cost make them perfect for mass production.
- The result is increased productivity.
- Time spent waiting is cut down when an automatic loading and unloading station is present.
- On the flip side, they are more costly.
Differences Between Watt
There are 4 different types ofbest laser welding machines available. Check out our extensive selection:
1. Laser welding machine 100w
2. Laser Welding Machine 200w
3. Laser welding machine 300w,400w,500
4. Laser Welding Machines 1000w including 1500w, 2000w - Kilowatt Laser Welding Machines
FAQ:
1. Which laser is best for welding?
Continuous lasers are the way to go when you need to weld thick materials. It works wonders on hard-to-melt metals. Use on metal or on an overly thin component can cause issues. Although it's more expensive than a pulsed laser, it saves money in the long run.
2. How do I choose a welding machine?
- Determine the metal's structure. The only other metal that is ever welded to is carbon steel.
- Find the ideal amperage.
- Find a good spot to do the welding.
- Find out what it can do by reading the technical specifications.
- Determine the need for compressed gas, if any.
3. What are the basic requirements of laser welding?
In laser welding, a highly concentrated beam of light is used as the heat source, and a lens is used to achieve this high directivity and convergence. By controlling the intensity of the laser beam, it is possible to perform penetration welding with a very small weld bead.
4. What two types of lasers are used for welding?
Therefore, the types of lasers used for laser welding can be generally divided into gas lasers or solid-state lasers.
5. How much does laser welding cost?
Automatic CNC laser welding machine with fiber laser powers of 1000W, 1500W, and 2000W can be purchased for between $18,800.00 and $25,800.00. The 1000W, 1500W, and 2000W fiber laser power supplies found in the reasonably priced. Visit out website for further pricing details.